When applying stamping lubricant, do you just Spray and Pray?
Years ago you probably had a trouble job and unless you flooded the tool, the lubricant just didn’t do the job. You may have even invested in a bigger or more powerful lubricant delivery pump or switched to larger nozzles to maximize flow. But what about the economics? How does your shop look? How does it smell?
In this case, more really isn’t better. Applying more of the wrong lubricant is not the best fix.
First – make sure your lubricant technology is current. There has been a lot of innovation over the years and some technology actually works better if you use less and not more. Really.
Second – a simple but easy way to control volume is nozzle size. Smaller nozzles put less on. It’s a fact. Size does matter. With newer polymer technology, you only need 1/3 the nozzle size. It’s a fire hose vs a garden hose.
At the tip of the nozzle you can find out the flow rate. The nozzle on the left is rated at 2 gallons per minute. The nozzle on the right is rated at one half gallon per minute. Big difference.
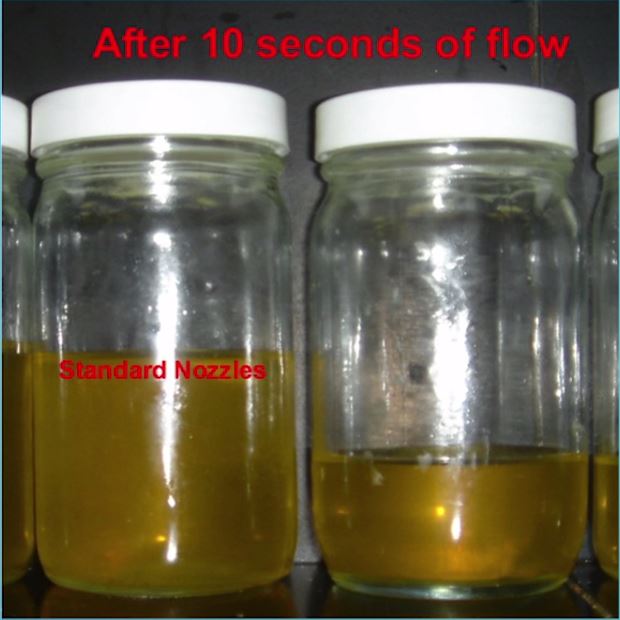
Don’t believe this matters? Look at the lubricant flow of a 2 gallon per minute nozzle vs a 1 gallon per minute nozzle.
But smaller nozzles clog right? Only if you use a soluble oil or don’t filter properly. Those oil free polymers I mentioned earlier don’t have that problem.
Perhaps your current supplier is happy that you are wasting lubricant. Maybe they’re even praying you don’t fix the problem at all.
Is that the kind of lubricant supplier you want? Is that the kind of lubricant supplier you deserve?
Give IRMCO a call. Problem Solved